PROFINET y OPC UA. Mantenimiento predictivo en planta Audi Alemania.
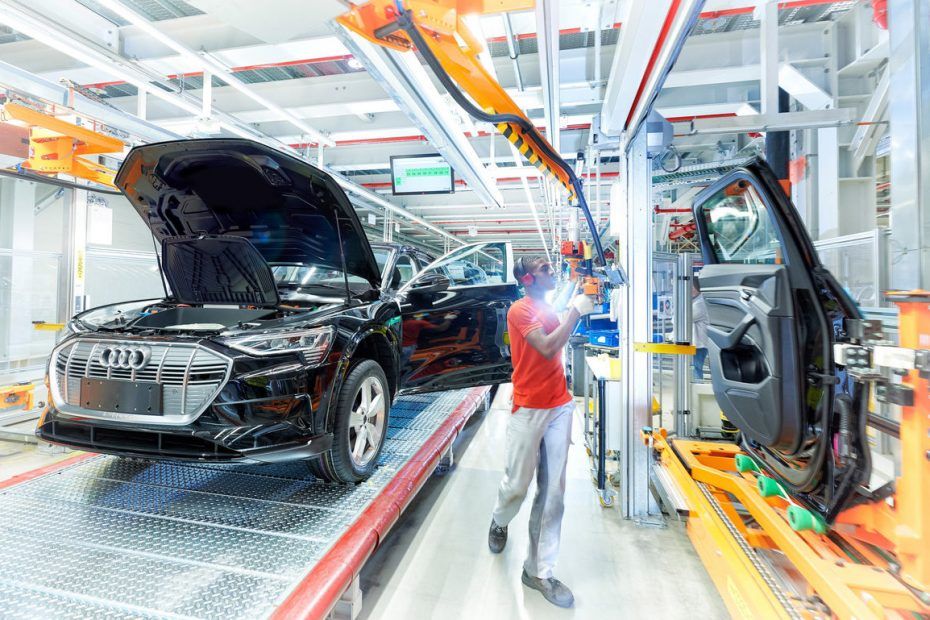
Hoy en día escuchamos hablar de mantenimiento predictivo, y quizás es algo que deberían manejar las fábricas para alcanzar ahorros significativos en paros innecesarios. Sin embargo, cuando se trata de implementarlo en la práctica, muchos técnicos e ingenieros a menudo fallan porque no tienen acceso a los datos correctos. ¿Cómo implementar PROFINET y OPC UA en un caso práctico?
Te compartimos la historia de Mathias Mayer en la armadora Audi en la ciudad alemana Neckarsulm.
Mathias Mayer se enfrentó a esta situación. Su experiencia le dice que "el 90 por ciento de los datos generados en la construcción del cuerpo [del auto] no se usan ni son accesibles". Y esto normalmente lleva a la necesidad de requerir un sensor adicional. Pero ese no era el camino que Mayer quería seguir. Por el contrario, pensó: "Primero procesemos los datos no utilizados. Si realmente fuera necesario un sensor adicional, sin duda estaría dispuesto a solicitarlo ".
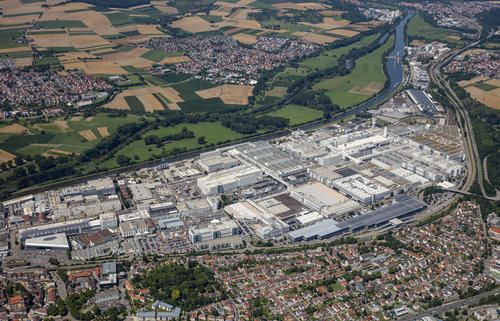
Para Mayer, darle un mejor uso a los datos que se encuentran disponibles, es el requisito más importante para reducir los tiempos de paro y trabajar de manera más eficiente. Este será un factor aún más decisivo, ya que la complejidad de los procesos de producción y el grado de automatización seguirá aumentando en el futuro.
Un mejor uso de los datos permite trabajar de una manera más eficiente.
Mathias Mayer.
Sin embargo, ¿por qué es tan difícil la tarea de recopilación de datos? Un vistazo al proceso de fabricación del cuerpo en la planta de Neckarsulm revela el desafío.
En esta planta son ensamblados los modelos A4, A6, A7, A8, R8 y A5 Cabrio. En el proceso intervienen alrededor de 2.500 robots industriales. Cada sistema es controlado por un PLC. "Siempre vemos al PLC como un maestro de marionetas que hace bailar hasta diez robots", dice Mayer al describir la situación en su área.
La creación del valor real tiene lugar en el robot, por lo que el acceso a los datos del robot es inmensamente importante para Mayer.
Los diferentes métodos de producción que se utilizan son un factor que dificulta el acceso a los datos.
Si se desea reducir el peso manteniendo la máxima durabilidad, solo se puede lograr combinando diferentes materiales. Esto implicaría el uso de diferentes tecnologías. Por ejemplo, actualmente se usa una gran cantidad de tecnologías de unión solo para el nuevo A8. Estas tecnologías van desde una muy amplia variedad de procesos de soldadura hasta el pegado y el remachado: en total, se deben coordinar 15 procesos diferentes. Si la producción falla, se necesitan expertos en cada uno de estos procesos individuales. Esto termina siendo muy costoso y requiere mucho tiempo cuando se considera la producción de tres turnos, ya que una gran cantidad de empleados necesitarían estar capacitados y calificados.
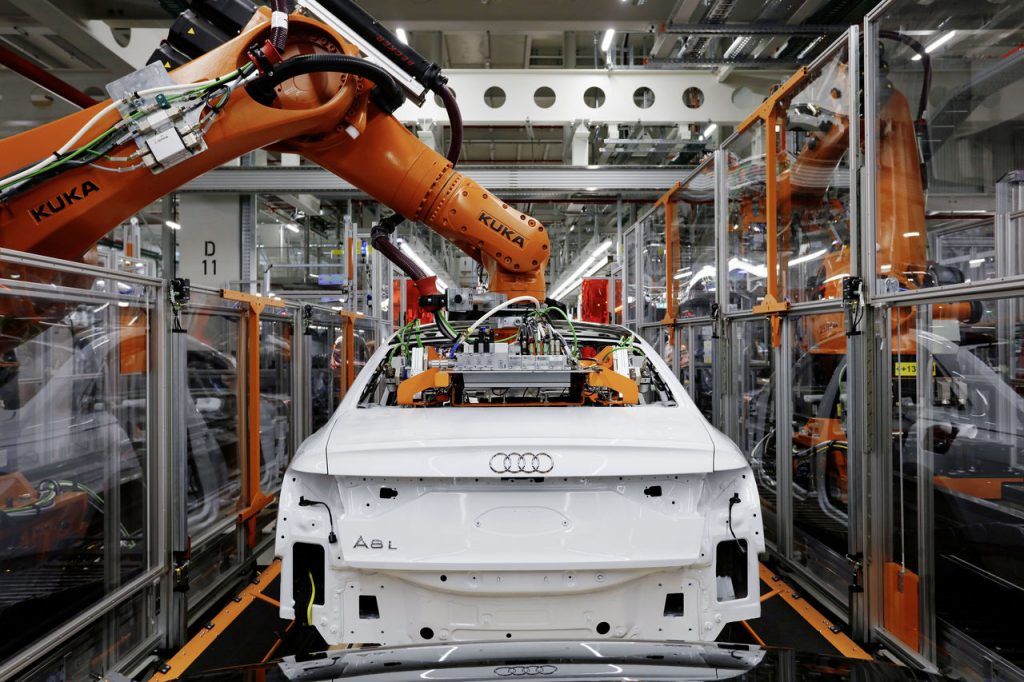
Explorando nuevos caminos.
Para Mayer, desviarse de los procesos que ya están probados es imposible. "Nuestro proceso de calificación es definitivamente costoso y requiere mucho tiempo, pero nuestros clientes esperan la mejor calidad". Con el simple hecho de hacer que diferentes empleados supervisen algo, se pueden producir resultados diferentes, pero si se lograran examinar los datos, los resultados serían siempre los mismos. "Es precisamente esta información la que tenemos que usar para optimizar tanto la producción como los procesos", dijo Mayer con convicción. Para este propósito, los datos del proceso deben analizarse de tal manera que incluso un "no experto" pueda volver a iniciar un proceso de soldadura por fricción sin complicaciones.
De esta manera, se reducirán los tiempos de paro no planeados del sistema de producción y se aumentará la disponibilidad, la eficiencia y la calidad del proceso.
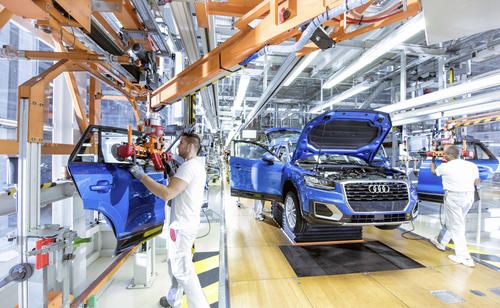
Implementación en aplicaciones prácticas.
Sin embargo, ¿cómo funciona esto realmente en la práctica? En un futuro se planea tener una cadena de procesos para la construcción del cuerpo del auto. Los datos correspondientes de los dispositivos se recopilarán, integrarán y visualizarán directamente, sin puertas de enlace adicionales, ya que, en última instancia, los robots tienen suficiente capacidad. Al final, hay un empleado que comprende el proceso y puede intervenir si es necesario. En opinión de Mayer, esta división del trabajo es la clave del éxito. Es solo sobre esta base que la minería de datos y el aprendizaje automático se pueden implementar con éxito.
En la arquitectura de Audi, OPC UA y MQTT se utilizan como medio de transporte de datos, que se enruta a una capa sobre la cual se encuentra una plataforma de Big Data. Además, se pueden colocar aplicaciones como análisis de diagnóstico para el monitoreo de condición y análisis predictivo para el mantenimiento basado en la condición.
Esta ruta también se establece en la especificación complementaria PROFINET OPC UA, cuyo contenido esencial incluye la recopilación y presentación de datos de diagnóstico y gestión de activos. Para este propósito, los datos de activos y diagnósticos de los dispositivos empleados hoy se recopilan en un controlador del sistema a través de los servicios PROFINET existentes y se entregan a instancias de nivel superior por medio de OPC UA.
La apertura de PROFINET permite, por ejemplo, agregar sensores con una interfaz OPC UA que envían sus datos directamente a los servicios en la nube correspondientes o puertas de enlace sin necesidad de reconstruir tediosamente la solución de automatización. Esto hace posible implementar métodos de diagnóstico innovadores, incluso en los sistemas existentes.
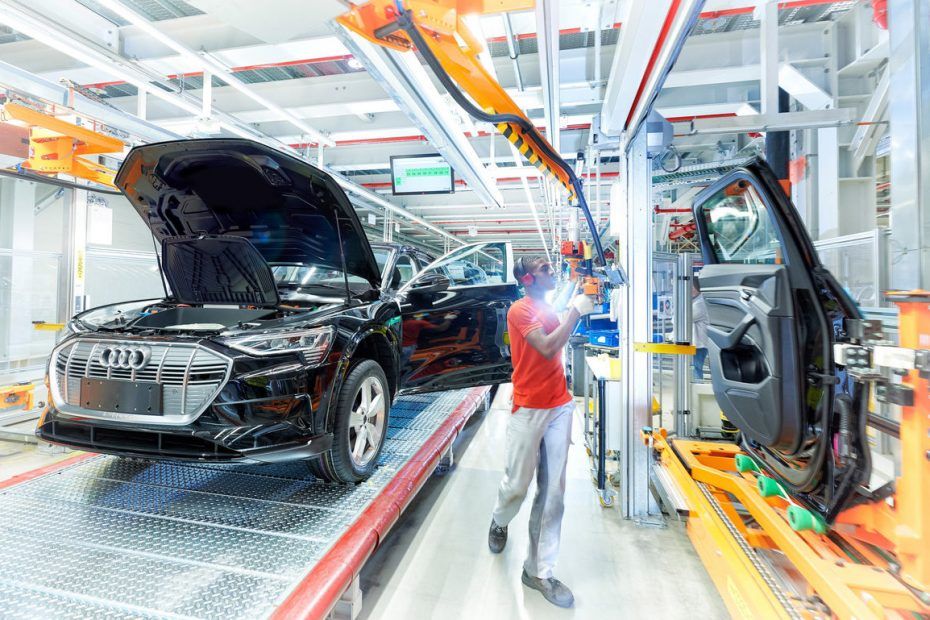
Todo el camino hasta el fondo.
Es una situación que también se conoce en la construcción del cuerpo del auto. “Para nosotros, un robot es simplemente un dispositivo subordinado del PLC. Nos gustaría penetrar hasta los datos en la parte inferior, pero no queremos establecer una red separada ", dijo Mayer, quien inmediatamente proporcionó una explicación pragmática. "Si se tiene que tender un cable adicional a más de 2.000 robots, simplemente no es viable. No solo esto, sino que no solo utilizamos un solo fabricante de robots. Dependiendo de la aplicación, confiamos en una gran cantidad de fabricantes diferentes [de robots]".
Además, OPC UA no ha sido implementado por todos los fabricantes. Todavía hace falta en las tecnologías más importantes en la construcción del cuerpo, como la soldadura por puntos, soldadura de pernos, pegado y remachado. En contraste, los fabricantes de los robots ya tienen un buen avance, al igual que los fabricantes de RFID.
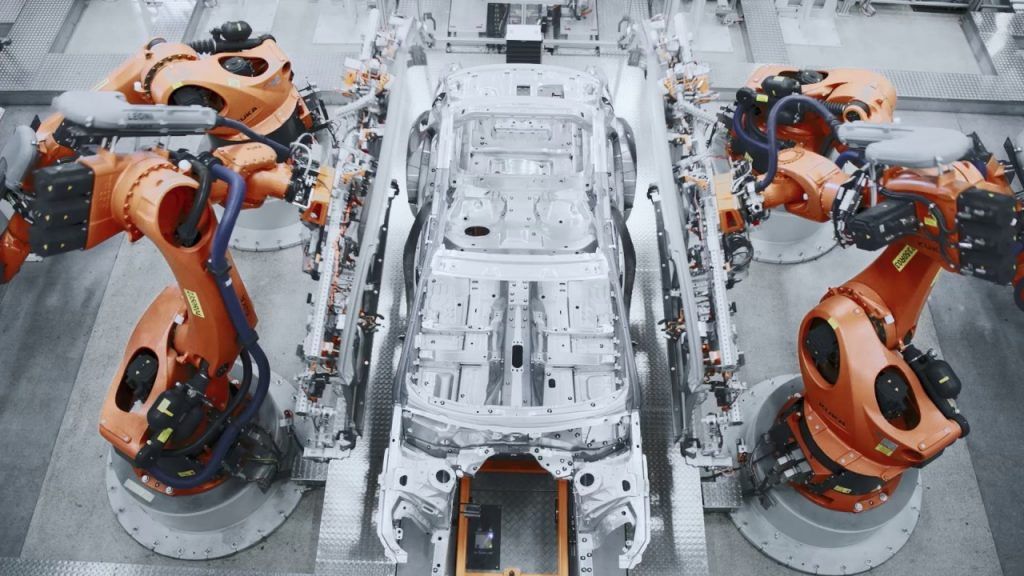
Implementación práctica.
En la implementación práctica, una cosa está clara: en aplicaciones donde ya se ha introducido una combinación de PROFINET y OPC UA, las ventajas surtieron efecto rápidamente.
Un buen ejemplo en la planta de Audi en Neckarsulm es el sistema de medición en línea para la alimentación de remaches sobre una manguera altamente flexible desde el área de llenado hasta la herramienta de remachado en un brazo robótico.
El desafío aquí radica en la velocidad de cierre del remache, que es relativamente alta, aproximadamente a 20 metros por segundo.
La manguera debe reemplazarse entre 500,000 y 1 millón de remaches. Ahora, la manguera ya no se debe reemplazar durante la producción, sino en el momento más conveniente, ya que el proceso debía pararse durante 20 a 30 minutos para cada cambio. Luego, el equipo creó un análisis de series temporales para detectar el desgaste en la manguera de alimentación. La implementación fue relativamente fácil: fluye más aire a través de la manguera tan pronto como pequeños poros comienzan a aparecer en ella. Estos resultados se registran, se envían por PROFINET a través de OPC UA en tiempo real y se visualizan.
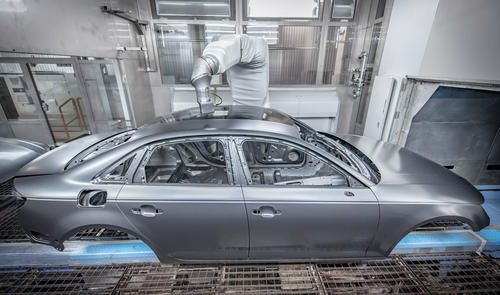
Ahora, cada empleado tiene la capacidad de enterarse de los eventos que tienen lugar en el nivel más bajo y tomar medidas más rápido, incluso sin un cable adicional.
Mayer espera que los nuevos requerimientos sean implementados pronto por los fabricantes de dispositivos. Al mismo tiempo, también les recuerda a los usuarios que tampoco deberían esperar demasiado. “Si deseas obtener beneficios en la producción, debes involucrarte con este tema desde el principio. Desde mi punto de vista, la Industria 4.0 ya llegó a la práctica desde hace un tiempo. Todo lo que tenemos que hacer ahora es implementarla".
Video: Reducción de complejidad en Audi.
Por último, te dejamos este video donde explican cómo se reduce la complejidad de los procesos en la Armadora Audi.
Reduced complexity in production at AUDI AG in Neckarsulm
"With our new standard we have created a modular solution set. In principle we can cover the entire production hall with solutions encompassing Software, Hardware and Drive components. This avoids complexity but allows us to react flexibly." Dr. Michael Niemeyer Head of Automation Technology AUDI AG, Neckarsulm http://www.siemens.com/tia
Vía: profinews.com
Deja un comentario